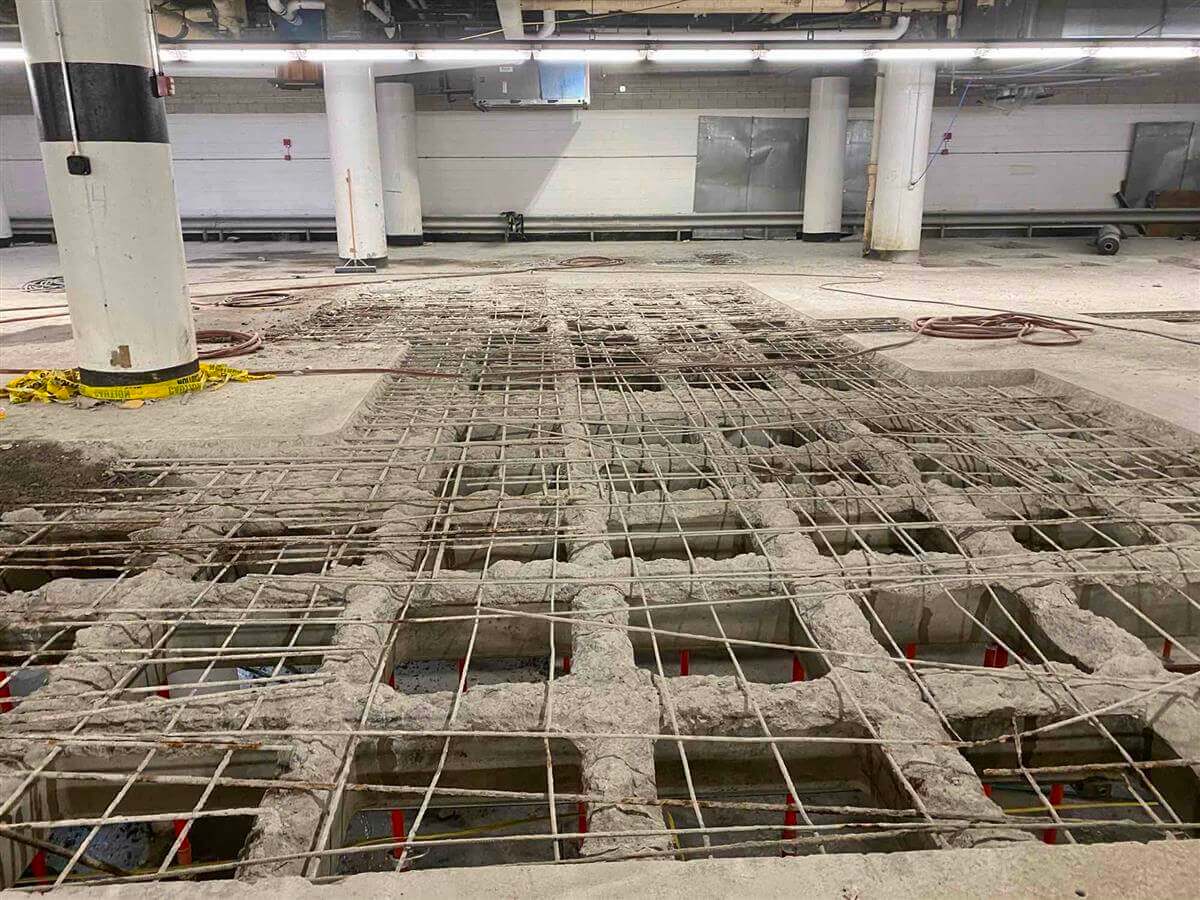
Private companies typically own a vast quantity of existing concrete infrastructure. Companies producing electricity utilizing different fuels have a variety of critical structures. These include reactors, turbine buildings and cooling water structures. In addition to electrical utility owners, major petrochemical owners also have critical concrete infrastructure such as jetties, pipelines, buildings, and support structures.
These critical concrete components are often taken for granted as their life expectancy is typically assumed to be indefinite. Unfortunately, this mindset tends to generate a lack of maintenance planning vital to structures in the day to day activities in the plants.
In reality, concrete structures have a life expectancy similar to that of a valve, pump, or like component. But, while the documentation of a pump is considered important because we understand it has an expected life which needs to be maintained in order to prevent plant down time, concrete structures typically are not documented as they are presumed infallible.
While complete failure of the concrete often is not an issue, degradation and damage which could lead to unexpected expensive repairs is a concern. Nearly the entire concrete infrastructure within a facility is important and encouraging senior managers to adopt a whole of life cycle approach toward these structures is key in providing durable structures.
Additionally, changing the way we think about our concrete structures will inevitability save money and minimize the cost necessary to achieve the design life of the structure. Managing concrete assets has to have a rational and systematic approach for organizing and implementing all the activities related to planning, constructing, maintaining, repairing, rehabilitating and replacing these structures. Doing so provides the maintenance manager the tools necessary to manage properly the concrete assets of the facility.
To gain a basic understanding of concrete structures, the first step is to adopt a rating system with a minimum of five states as shown in Table 1. A five state system has proven to be a practical and accurate method of condition management. The ratings should be based on measurable amounts of damage to the existing structure.
Condition Rating Definition | |
0 |
Initial state, no degradation. |
1 |
1/3 of limit state. |
2 |
2/3 of limit state. |
3 |
Limit state. |
4 |
Post limit state. |
Table 1 – Condition Rating Definition
By defining the conditions of our structures in accordance with table 1, we can start to manage a whole life concept by carrying out the following:
- Define current condition
- Plan ongoing monitoring to enable rating of the structures
- Recommend solutions for maintenance and repair
- Predict and prioritize structures in need of maintenance and repair
- Forecast budgets needed to maintain the structure
- Document and formulate the structures condition against time
This list enables us to follow a process where we continuously assess the condition, predict and model the performance against time and evaluate the durability/reliability of the structure. Managing the structure in this manner allows the engineer to produce a decision-making procedure on how to maintain and repair the structure through its lifespan.
Understanding Predictability and Reactive Repair
Understanding the predictability of structures means that the performance of the structures and the financial needs for maintenance, repair and rehabilitation are managed and predicted by the system utilized to manage the asset.
Unfortunately, most maintenance plans work reactively in that the repairs are performed as a reaction to the needs observed during failure or when health and safety concerns arise. No preplanning is used and an enormous burden on budgets can occur as the costs are unknown.
By managing the asset, the engineer can predict the performance of the structure based on its current condition and predict the financial needs for maintenance on a long or short-term basis. This technique will often provide alternative technical strategies for the asset over the expected design life.
Typically, when new structures are built a probabilistic approach is used in demonstrating the design life of the structure. Existing structures can also adopt this probabilistic approach by using degradation models to determine their reliability, serviceability and safety. This approach also helps deal with uncertainty and structural risk. Using current technology, more accurate tools can be developed for decision making and risk analysis – allowing management to budget and plan for maintenance and repairs.
Life Cycle Management
Changing from the reactive approach to the predictive approach also means that the implementation of life cycle technology has to be adopted by the facility management. Regardless of the age of the structure, when this approach is adopted an improved sustainable structure is created
The life cycle management procedure provides a systematic approach for organizing and implementing all the activities related to planning, constructing, maintaining, repairing, rehabilitating and replacing structures. This process is typically broken into two main parts for management purposes: Part 1 – Facility Management and Part 2 – Project Based Engineers and Managers.
The objective of Part 2 is to make the necessary decisions based on the results of the inspection of structures and the execution of maintenance and repairs. Within this part of the process, project based engineers and managers should be able to answer the following:
- Which structures should be repaired?
- Which maintenance and repair methods should we use?
- When do we carry out the maintenance and repairs?
Project based engineers and managers need to gather the information necessary for analyzing structures and use that data to develop maintenance and repair plans. By combining the projects and the required maintenance and repair actions, the annual plan for managing the structures can be formulated for Facility Management.
This facility management then provides the overall administration of the facility and can evaluate the appropriate level of funding to maintain the performance of the structures at a desired safe and economic level.
Maintenance Policy
The maintenance policy, as defined by Facility Management, has to define the requirements for the upkeep of the structures under a policy that clearly defines strategic targets, as well as potential financial constraints.
Strategic targets may be categorized as follows:
Control of condition
- Preservation of assets
- Striving to an optimal condition level
The main objective of the maintenance policy is to keep a steady-state condition of the structures in order to preserve its asset value. The long-term goal for management is to analyze and maintain an optimum condition for the structure. The short-term goal is to define the yearly steps for determining an unacceptable condition state at which the maintenance and repair cost is assumed to be minimal.
Control of usability
- Safety, security, health and comfort
- Functionality and serviceability
Structural safety is generally controlled by condition constraints where a minimum allowable condition is defined. If the structure exceeds this condition, a maintenance and repair action should take place. Performing a capacity and safety analysis is another way of managing the safety of the structure – with the possibility that results may trigger actions such as strengthening or replacement.
Functionality and serviceability are also controlled by condition constraints and by a structural serviceability analysis. The lowest tolerable condition states based on functionality or serviceability requirements are often decisive when compared to those based on structural safety. In a predictive management system, functionality and serviceability are strongly related to the obsolescence of assets.
Control of costs
- Life cycle costs: maintenance, repair, rehabilitation, renewal and demolition costs
- Operating costs
- User costs in operation
As a result of a life cycle cost analysis, optimal life cycle actions can be identified. Not only heavy repair actions, but also protective maintenance actions can be considered in the life cycle cost analyses. Necessary elements of the analyses are the degradation, repair action and cost models of structures.
The optimization of life cycle costs includes optimal timing of actions which can be done by specific degradation models when the limit condition state is known. An effective asset management plan includes the possibility for minimizing the delay costs. The delay costs are the result of deferring maintenance and repair actions from the optimal time. The delay costs are often decisive when prioritizing actions and projects.
Failure costs can be defined as the product of the probability of failure and the capital consequences of a failure. Failure means either exceeding the serviceability limit state regarding performance requirements, obsolescence or the ultimate limit state. The costs of the consequences of a possible fatal failure would be by far greater than just the repair costs.
Case Study
At a major facility in south central Texas, the concrete cooling tower for the plant was suffering from significant corrosion after 29 years of operation. Electro Tech CP was employed to investigate and document the condition and to provide a management program for long term maintenance and repair.
The major walls of the cooling tower were extensively investigated to establish the underlying levels of corrosion activity. This process was carried out by utilizing a half cell potential survey which determines the corrosion potential of the steel.
In combination with the half cell survey, a limited amount of additional testing was carried out and more emphasis was applied to diagnosing the collected data. The objective was to determine the following:
- Identify the cause or causes of the defects
- Establish the extent of the defects
- Establish where the defects could spread
- Assess the effect of defects on structural safety
- Identify all locations where protection or repair may be needed
In assessing the structure, it was apparent that repairs would be needed to prevent the loss of the structure. The evaluation also indicated that all chloride samples exceeded ACI requirements, carbonation levels were very low and all compressive strength values exceeded the design requirements.
This information provided sufficient evidence that the cooling tower would continue to fail over a very short time period – producing additional concrete failure of some 10,000 square feet. The data was pivotal in the decision to provide a long-term mitigation plan.
The management process for the towers was broken down into repair options and selection rationale. All information was considered and a series of questions and answers was developed in accordance with current standards, industry knowledge and research.
To identify the most suitable repair rationale, a selection strategy was adopted which incorporated all of the data collected during the condition assessment and all other key influential factors. The repair selection was broken down as shown in Table 2.
Number |
Option |
1 |
Do Nothing |
2 |
Analyze Structural Integrity |
3 |
Reduce Further Deterioration |
4 |
Improve/Refurbish All or Part |
5 |
Reconstruct All or Part |
6 |
Demolish All or Part |
Table 2 – Repair Options
From there, the client’s requirements for the repair proposal incorporated a selection rationale based on Table 3.
Number |
Rationale |
1 |
Intended Use, Design Life and Service Life |
2 |
Performance Characteristics Requirements |
3 |
Long Term Performance of Protection or Repair |
4 |
Opportunities for Additional Protection or Monitoring |
5 |
Acceptable Number of Repair Cycles and Cost |
6 |
Future Maintenance and Access Cost |
7 |
Structure’s Appearance |
Table 3 – Selection Rationale
The rationale adopted was based around the repair option methodology of items 2, 3 and 4 shown in Table 2. Due to the extent of delamination and the scale of repairs, a structural assessment was necessary to determine the phasing of the repair.
In addition to the repair options, each of the criteria from Table 3 was evaluated to develop the rationale. The major factor in this analysis was the shear scale of the corrosion problems and how that impacted the client’s need for a long-term repair and along with additional protection in the use of cathodic protection.
Using this information and the knowledge of the client requirements, a plan for the strategy, principle and method was formulated as shown in Table 4.
Strategy |
Reduce Further Deterioration and Improve the longevity of the structures |
Principle | Analyze Structural Integrity, carry out full-depth concrete repair and install an Impressed Current Cathodic Protection (ICCP) System for the shell and a Sacrificial Cathodic Protection (SCP) system for the column legs. |
Method |
Analyze Structural Integrity, carry out full depth concrete repair and install an Impressed Current Cathodic Protection (ICCP) System for the shell and a Sacrificial Cathodic Protection (SCP) system for the column legs. |
Table 4 – Planning
Summary
Managing concrete assets is increasingly becoming a responsible method for ensuring long-term sustainability of structures. While not a new concept, it is generally one area which does not get the attention needed to provide long-term cost-effective maintenance. Planning early and understanding the current condition of your structures is essential to providing cost effective solutions over the life expectancy of the structure.